CASE STUDIES: Health/Safety
|
Companies across the nation rely on standards and conformance to increase efficiency, reduce cost, and boost market access for their products and services. Here are a few examples of how standards and conformance contribute to the health and safety of citizens worldwide:
|
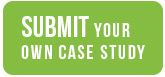 |
Standards and Conformance Keep Toys Safe, Build Consumer Confidence
In the summer of 2007, headlines across the country declared that toys on store shelves were unsafe. Lead paint was a key issue, as was the perceived lack of testing and inspection done by manufacturers and regulators alike, in this case the U.S. Consumer Product Safety Commission (CPSC).
What went wrong? Who was to blame? And how can we quickly fix the problem? These questions were the focus of much media interest, consumer concern, and congressional attention.
As S. Joe Bhatia, president and CEO of the American National Standards Institute (ANSI), stated during a congressional hearing in September 2007, “This hearing is
necessary not because there is an issue with existing standards, but because some suppliers – particularly those who are exporting products to U.S. soil – are not complying with the rigorous standards and regulations that have been established to keep our citizens safe.”
In other words, strong toy safety standards had been in place, including ASTM International’s F963, which was introduced in 1986 and is subject to a continuous review process to address potential emerging safety issues and new product features. But manufacturers and suppliers – many operating overseas – were
not complying with safety standards. They were not holding their products up to the appropriate quality control measures. And because the CPSC had been relying upon manufacturers to complete the appropriate testing and conformance procedures, the CPSC was not prepared or staffed to handle all the inspection
duties that the public, media, and congress felt it should be taking on.
In the wake of this crisis of confidence, the standardization community sprang into action, and three key solutions arose:
- ANSI and the Toy Industry Association (TIA) together formed the Toy Safety Coordination Initiative (TSCI) to put
in place immediate recommendations for more comprehensive and effective toy safety conformance measures. ANSI and TIA also collaborated on the Toy Safety Certification Program (TSCP), where ANSI was named the official third-party accreditor of TSCP’s product certification bodies.
- The Consumer Product Safety Improvement Act of 2008 (CPSIA) – focused heavily on children’s products – mandated that toys and other children’s products be tested for compliance by a third-party CPSC-accepted laboratory (as opposed to the
CPSC performing testing duties itself).
- The CPSIA also specifically cited ASTM F963 as the mandatory consumer product safety rule for all toys sold in the United States.
Given the nature of the toy business – with constant innovation and a complex global supply chain – it was especially key that safety solutions focus on private-sector leadership. The U.S. CPSC has no authority to
inspect manufacturing facilities in foreign countries, and not enough bandwidth to inspect all toys shipped into the U.S. for sale. But by relying upon nimble, consensus-based, private-sector standards, and by relying upon recognized third-party testing rather than just
taking a supplier’s “word for it,” a much stronger and more effective toy safety system has arisen. Today’s consumers trust in the safety of toys on store shelves, and that confidence speaks to the power of private-sector standards and conformity assessment.
– American National Standards Institute.
ASME (the American Society of Mechanical Engineers) has developed codes, standards and conformity assessment programs for over 125 years to guide
engineers and regulators in creating more efficient and safer production and work environments. One code in particular, the ASME Boiler and Pressure Vessel (BPV) Code,
is often utilized at nuclear power plants and contributes to safer, cleaner and more profitable energy production. By following the ASME BPV Code, many companies,
including Dominion Resources, have saved millions of dollars by enhancing safety protocols and keeping their equipment running at high efficiencies.
One of the nation's largest producers and transporters of energy, Dominion has saved tens of millions of dollars in avoiding unwanted repairs, time delays, outages,
and lost revenue by implementing Section XI of the ASME BPV Code, which focuses on in-service inspection of nuclear power plant components. And every ten years Dominion
saves $2.6 million from a nuclear safety innovation called Risk-Informed ISI that was generated for the code specific to piping welds. Section XI has changed the way
inspections are performed on piping welds, making the process more efficient and less time consuming. This has not only saved Dominion millions of dollars, but has enhanced
productivity and safety throughout the nuclear industry.
Dominion has seen significant cost savings, increased efficiencies, and improved safety measures through its use of the ASME BPV code. By following these requirements
and guidelines, Dominion is able to help keep their employees safe and provide a more efficient work environment.
Want to learn more? Check out the full-length case study.
– ASME; Dominion Resources
From 1999 to 2002, approximately 15,300 fires occurred annually where the first item ignited was a mattress and its bedding. These fires resulted in an annual average of 350 deaths, 1,750 injuries, and $295 million in property loss. In an effort to reduce deaths and property damage, the U.S. Consumer Product Safety Commission (CPSC) and the National
Institute of Standards and Technology (NIST) joined forces to establish flammability standard 16 CFR Part 1633 .
The mandatory standard is designed to reduce the severity of mattress fires ignited by open flame sources such as candles, matches, lighters, and cigarettes. The CPSC estimates that 16 CFR Part 1633 prevents as many as 270 deaths, 1,330 injuries, and millions of dollars in property damage every year.
Want to learn more? Check out the
full-length case study.
– National Institute of Standards and Technology, U.S. Department of Commerce
According to the U.S. Consumer Products Safety Commission (CPSC), during the 1980s electrical arc faults were associated with more than 40,000 home fires, claiming over 350 lives and causing 1,400 injuries annually. In 1992, the electrotechnical industry developed an Arc Fault Circuit Interrupter (AFCI) which continuously monitors current flow.
They worked with Underwriters Laboratories to publish UL 1699, Standard for Safety of Arc-Fault Circuit-Interrupters, in 1996 which provides testing, performance, and construction requirements for this critical equipment. AFCIs are also a requirement in the National Electrical Code (NEC), the model code for electrical wiring developed by the National Fire Protection Association (NFPA).
Standards and conformity assessment activities for AFCIs help protect against hazardous arc faults, saving lives and protecting property nationwide.
- National Electrical Manufacturers Association (NEMA)
South African hotel and entertainment management company Tsogo Sun Group faced the challenge of preparing workers and enhancing facilities for natural or man-made hazards that might arise during the 2010 Federation Internationale de Football Association (FIFA) World Cup. American National Standard ASIS SPC.1-2009, Organizational Resilience: Security, Preparedness, and Continuity Management Systems - Requirements with Guidance for Use, was chosen as the most comprehensive management systems approach for security, preparedness, response, mitigation, business/operational continuity, and recovery for disruptive incidents resulting in an emergency, crisis, or disaster.
Rather than pursue third-party certification due to time and cost constraints, the hotel group established an internal team to execute rigorous auditing of the implementation of the standard. The team completed the ISO 28000 Lead Auditor Course, the same course required for third-party certification body auditors. After communicating project goals company-wide and soliciting input from employees at all levels of the organization, a six-level phased implementation was coordinated engaging all employees. The phased approach with a framework of steps made implementation more manageable, resulting in maximum buy-in and compliance. The process ensured that gaps were addressed and previous work was integrated into a focused and comprehensive plan for organizational resilience.
Want to learn more? Check out the full-length
case study.
– ASIS; Tsogo Sun Group
In the 1970s, hospitals began using computers to process digital medical images. Initially, most devices stored images in a propriety format and transferred these files over an internal network or on removable media. These incompatible systems made images inconsistent and sharing information difficult, expensive, unreliable and inefficient. In order for physicians, hospitals and patients to fully reap the benefits from digital medical images and information, the medical community called for interoperability and a standard method for transmitting medical images and their associated information.
In 1983, the American College of Radiology (ACR) and the National Electrical Manufacturers Association (NEMA) formed a joint committee to create a standard method for transmitting medical images and their associated information. Within ten years the standard grew to utilize computer network standards and was renamed Digital Imaging and Communications in Medicine (DICOM). DICOM includes standards not only for images but also for patient records, studies, reports and other data groupings, and has contributed to improvements in image quality and presentation consistency.
The DICOM standard permits the transfer of medical images in a multi-vendor environment; provides a strong base for developing and expanding picture archiving and communication systems; and supports interfacing with medical information systems. DICOM is utilized in virtually every medical profession that uses images including cardiology, dentistry, endoscopy, mammography, ophthalmology, orthopedics, pathology, pediatrics, radiation therapy, radiology, surgery, as well as veterinary applications. As patient information transfers to digital forms, all Electronic Health Record (EHR) systems that include imaging information as part of the patient record will require DICOM.
Ultimately, the benefit falls to the patient. Physicians have better access to images and reports allowing them to make a faster diagnosis, potentially from anywhere in the world. As a result, patients can obtain faster, more effective care.
- The DICOM Standard’s Development and Maintenance is Managed by the Medical Imaging & Technology Alliance (MITA), a division of the National Electrical Manufacturers Association (NEMA)
Following the terrorist attacks of September 11, 2001, there was an increased focus on using x-ray and gamma-ray screening technologies for homeland security applications. However, the international community found itself at a loss for comprehensive performance standards against which these technologies could be evaluated.
In 2005, the Department of Homeland Security (DHS) and the National Institute of Standards and Technology (NIST) launched an effort to identify and develop national voluntary consensus standards for the use of x-rays and gamma rays in the screening of carried items and human subjects at airline checkpoints, airline checked baggage, air cargo, and other venues, as well as the associated radiation safety concerns. The result was the development, renovation, and promulgation of x-ray safety (i.e., IEC 62523-2010, HPS N43.17-2009) and image performance (i.e., IEEE N42.44-2008, ANSI N42.46-2008) standards that significantly benefit passengers and users of air transportation services, government agencies, equipment manufacturers, and the international community – creating a safer air transportation infrastructure for all.
A conservative, rough-order-of-magnitude (ROM) estimate of the economic benefits associated with x-ray screening standards is in the hundreds of millions of dollars. For example, it is estimated that x-ray screening machines would be 40% more costly in the absence of consensus standards. If the average cost of an x-ray screening device is $300,000, and there are 6,000 in usage, an ROM estimate of savings to manufacturers is $720 million. And the total social benefits of air transportation security standards are higher since the ROM estimate only considers the direct beneficiaries of increased airline travel security.
The economic benefits of air transportation security also extend to indirect beneficiaries whose lives and business are more secure because air transportation is more secure, such as other potential terrorist targets like highrise buildings, nuclear power plants, and government buildings. In addition, significant efficiencies and savings are achieved by a reduction of the number of design versions of x-ray equipment as a result of common requirements, common measurement language, and common configuration controls provided by the standards.
- National Institute of Standards and Technology, U.S. Department of Commerce
The Dallas-Fort Worth Hospital Council (DFWHC) faced the challenge of linking millions of records from numerous different facilities using various information systems to create a cohesive patient-centric view of information. DFWHC was previously limited to analyzing information at the encounter rather than the patient level. This made it impossible for DFWHC to look at all visits for a single patient within or across entities and limited the ability to analyze data and identify trends.
DFWHC worked in partnership with QuadraMed to implement QuadraMed’s Smart I/X EMPI (enterprise master person index) software for record matching. This resulted in the ability to link inpatient to outpatient hospitalization encounters, link multiple outpatient encounters, calculate readmission rates, link research data to inpatient and outpatient databases, support research activity to improve healthcare delivery, track infections, and develop episodic metrics and analytic capability to evaluate chronic illnesses models.
DFWHC was ultimately able to link 7.4 million records from 136 hospitals, achieving a patient-centric view of inpatient and outpatient clinical information for research and reporting that can be used to evaluate and improve patient safety and care across the region. These advancements have led to the beginning stages of a regional health information exchange (HIE). And because the regional EMPI conforms to Integrating the Healthcare Enterprise (IHE) profiles, which organize and leverage the integration capabilities that can be achieved by coordinated implementation of communication standards, it can be expanded to manage a future HIE.
– Dallas-Fort Worth Hospital Council; Healthcare Information and
Management Systems (HIMSS) Integrating the Healthcare Enterprise (IHE)
Since its initial release in 1994, CP-01, Control Panel Standard –Features for False Alarm Reduction, has significantly contributed to the nearly 70 percent reduction in false intrusion alarms reported to law enforcement. Moreover, during the past 16 years, sales of new alarm system panels have doubled.
In the mid-1990s, the security industry was making huge technological advances in their residential and commercial security panels. However, market presence, consumer confidence, and law enforcement acceptance was undermined by the number of false alarms generated by user error. Among other issues, emergency buttons were too easily triggered, entry and exit times were being set to low, optional communication delays were not being utilized, and system resets were not sequenced properly after power failures. CP-01 addressed many of these problems, and the standard continues to be revised, most recently in May 2010, to meet ever-changing technological demands.
The CP-01 standard has not only allowed dealers, installers and monitoring companies to thrive in communities where local law enforcement had threatened to implement a non-response policy, it has also opened new business by boosting public confidence in the reliability of security systems and convincing officials in several areas to relax what had been very stringent response policies.
The success of the CP-01 panels in curtailing user errors and reducing false alarms was so profound that the National Sheriff’s Association and the International Association of Chiefs of Police passed simultaneous national resolutions recommending that all law enforcement jurisdictions require its use for new installations. As a result, hundreds of agencies have included such mandates in their ordinances, and at least three states have enacted laws requiring panels to be CP-01 compliant.
– Security Industry Association (SIA)
Industry standards used in tree care management provide the baseline knowledge for all our industry education and credentialing programs. In addition, they are used as the basis for most large commercial, municipal, utility, and governmental contracting.
These standards are so essential to the services our industry provides, it would be difficult for our organization or our member companies to place a concrete value on them.
– Tree Care Industry Association
In the 1980s, a new pipe-joining technology called a mechanically attached fitting (MAF) was developed, promising substantial improvements including easier fabrication, higher reliability, and lower costs over existing pipe-fitting technologies such as welding and brazing. But the Navy needed a universal test standard to verify the integrity of MAFs before authorizing their use in the fleet.
The Navy chose to work with industry to develop a non-governmental standard (NGS) for MAF testing: ASTM F1387, Standard Specification for Performance of Mechanically Attached Fittings, a flexible but stringent commercial performance standard that addresses all potential MAF designs. These efforts enabled the Navy to adopt and use many MAF designs early and successfully with substantial savings, improved quality and safety, and increased productivity. By 1993, the Navy had used many approved MAFs with excellent results and saved millions of dollars in the first few years.
Several different cost studies show that the use of MAFs saves up to 50% of the installed cost compared with the use of welded or brazed fittings. A fitter/helper team can routinely install 50 to 60 fittings in a single shift, more than double the rate at which welded piping systems typically are shop fabricated. By eliminating welding, many overhead costs relating to safety, personnel, equipment and supplies, inspections, rework, and monitoring are eliminated or substantially reduced.
By expediting the development of the ASTM standard and engaging industry in validation, the Navy brought the new technology to the fleet faster, better, cheaper, and with greater choice of products. The Navy was able to leverage the industry resources rather than conducting the research, testing, and validating using its own resources resulting in a $1 million savings. As the Navy continues to qualify new MAFs and add new applications for MAFs, the recurring savings and cost avoidance continues to grow.
Want to learn more? Check out the full-length case study.
– U.S. Navy
MedCentral Health System in Ohio needed to streamline its chart abstraction functions to enable it to efficiently meet increasing federal and state core measures reporting requirements. They were looking for a tool that would integrate seamlessly into their current clinical and financial departments and ancillary information systems.
Previously, MedCentral had no data mining applications; they relied on manual chart abstractions. Manually abstracting information buried in many different systems from many different departments can swamp healthcare organizations and poses a serious obstacle to calculating and reporting core measures in a timely manner. And when patient-quality issues are identified, isolating contributing factors can be an arduous task, dramatically slowing down and impeding the ability of a hospital to correct quality problems.
MedCentral looked to Siemens Soarian® Quality Measures for a solutions. Soarian® Quality Measures uses Integrating the Healthcare Enterprise (IHE) and Healthcare Information Technology Standards Panel (HITSP) interoperability specifications in its methods for obtaining patient clinical information, and then evaluates and reports on quality measures based on that information.
By adopting the HITSP specifications and initiating use of EHR technologies, MedCentral’s core measures reporting requirements became less burdensome to facilities and enhanced the reporting processes. In addition, MedCentral experienced improved accuracy of chart abstractions and is now positioned to more effectively manage patient quality issues.
– Siemens; Healthcare Information and Management Systems (HIMSS) Integrating the Healthcare Enterprise (IHE)
In the post-9/11 environment, the U.S. Department of Homeland Security (DHS) faced public fears that a dirty bomb attack could cost billions of dollars, cause extensive environmental contamination, result in hundreds of fatalities and injuries, and take years of recovery. In response, DHS dramatically increased efforts to screen the vast amounts of cargo entering U.S. ports daily. While some of the equipment needed to monitor cargo was already on the market, it was not able to handle use in diverse settings, nor was it designed for use by non-specialists or first-responders.
In collaboration with DHS, industry, and other national laboratories, the National Institute of Standards and Technology (NIST) coordinated and integrated the work of the Institute of Electrical and Electronics Engineers (IEEE) Radiation Detection Standards Program N42 Committee to address radioactivity measurements, homeland security, and protection instrumentation for increased port security. The N42 Committee developed a suite of standards for radiation detection equipment from small, handheld detectors to massive, port-screening monitors that could be used easily by non-specialists and first responders to scan massive amounts of cargo for nuclear-radiological threats.
Today, users and vendors have access to standards that set performance requirements for radiation detection equipment based on homeland security needs; increase the effectiveness and efficiency of cargo, vehicle, and other screening processes; and reduce the risk of terrorist attacks on U.S. soil.
Want to learn more? Check out the full-length case study.
– National Institute of Standards and Technology, U.S. Department of Commerce
Health care information standards enable pathologists to create and share information in a manner that is cost-effective and of high quality, promoting patient safety and re-use of health care information.
– College of American Pathologists